
Utilization
Medium temperature water can be widely found in nature and in industrial processes, such as thermal drainage (e.g. steam condensate, chemical reaction drainage), power plant (e.g. generator jacket water), geothermal water, etc. Medium temperature water already has a certain temperature and can be used directly for cooling, heating or steam production.
Utilization Modes
Cooling
Hot water above 70°C can drive a hot water absorption chiller for cooling. If the temperature of the hot water is higher, then the chiller will be more efficient and the investment will be lower. The chiller model and cooling capacity can be determined based on the following table:
Type | Temp of Heat Source Water | COP | Output | Remarks |
Normal | 98/88 | 0.83 | 88% | Lowest Investment per unit cooling capacity |
90/80 | 0.76 | 70% | ||
Double Section | 90/70 | 0.72 | 55% | Most Application |
Double Generation | 70/55 | 0.5 | 55% | Less Competitor |
Triple Generation | 90/55 | 0.6 | 55% | Largest Cooling Capacity |
BROAD CHP System on Summarecon Mall Kelapa Gading
Mall Kelapa Gading (MKG) is the largest shopping center in Jakarta and the third largest in Indonesia, with a tenant area of 150,000 m², managed by PT Summarecon Agung Tbk. Located in North Jakarta, MKG stands out for its efficient power usage for cooling by utilizing absorption chiller technology. It uses gas engines for electricity, with exhaust gas and hot water from the engines as heat sources for absorption chillers, producing “free” chilled water for air conditioning, a system known as Combined Cooling Heating & Power (CCHP).
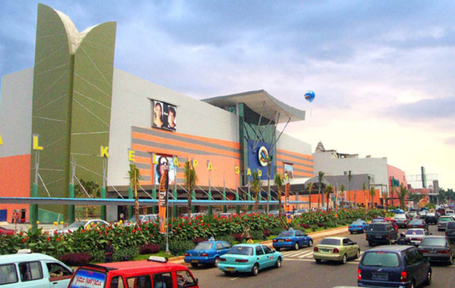
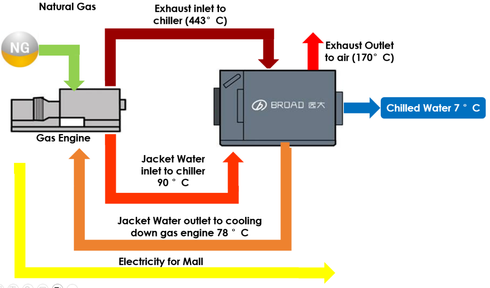
MKG is a shopping center that uses gas engines as their source of electricity, exhaust gas and hot water from the engines then used as heat source in absorption chillers to produce “free” chilled water for mall room air conditioning purposes. We call this kind of energy system Combined Cooling Heating & Power (CCHP).
In this case, Mal Kelapa Gading leverages waste heat from exhaust gases and hot water to produce chilled water at a temperature of 7°C. This combination effectively provides free cooling for the mall, as the electricity generated by the gas engine is used for mall operations while the absorption chiller serves as the cooling system. The exhaust gases, with an initial temperature of 443°C, are utilized to heat the chiller, and the exhaust outlet temperature is reduced to 165°C, ensuring the released air is clean and minimizes CO2 emissions. Additionally, hot water is used to further heat the absorption chiller. This hot water is sourced from the gas engine’s jacket water, and after being utilized at a temperature of 78°C, it is recirculated back to the gas engine for its cooling needs. This system is very effective for user because the heat is fully used for chiller and help the gas engine operates normally because the jacket water is cooling down by our chiller.
Cooling of Medium Temperature Distillation Cooling Water
Liuchixiang Distillery, Shiwan Distillery
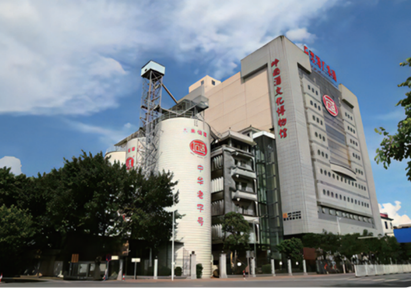
Liuchixiang Distillery in Yibin, Sichuan, with an annual production capacity of 25,000 tons of raw liquor, initially wasted energy and caused thermal pollution by directly discharging medium-temperature cooling water from 18 coolers. The cooling process relied on electric chillers, consuming significant electricity.
After upgrading to a hot water absorption chiller system, the distillery saved 130,000 tons of water and 732,600 kWh of electricity annually. Similarly, Guangdong Foshan Shiwan Distillery innovated its cooling process to handle high temperatures, resulting in substantial energy savings of 1.23 million kWh annually by using a hot water absorption chiller for cooling and air conditioning, instead of relying solely on cooling towers.
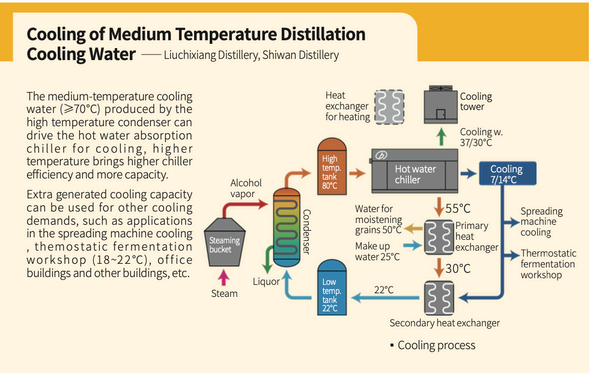
Dole Philippines, Inc.
Dole Philippines, Inc. (DPI) is a subsidiary of Dole Food Company, Inc., a leading producer and marketer of fresh fruits and vegetables. DPI was founded in 1963 as Standard Fruit Company (Stanfilco) and began commercial operations in 1968.
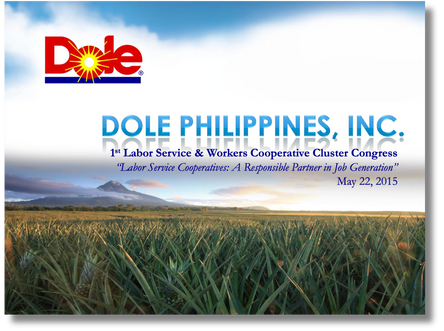
DPI operates 10 banana and pineapple plantations in Mindanao, Philippines, covering 30,000 hectares, with packing and processing facilities in General Santos City and Davao City, employing over 15,000 people and exporting fresh fruits globally under the Dole brand. Committed to sustainability, DPI has implemented environmental and community programs, earning awards like the Best Sustainability Initiative Award from the Philippine Chamber of Commerce and Industry.
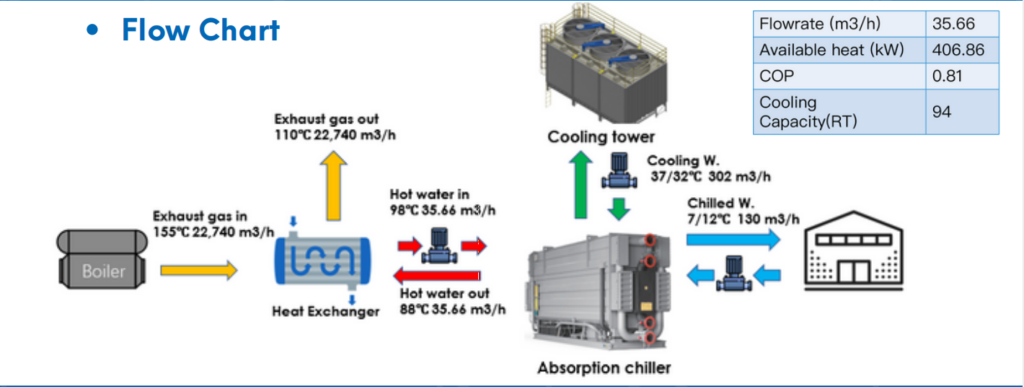
BROAD Chiller ROI For DOLE

Absorption Chiller | Air Cooled Chiller | |
Cooling Capacity(RT) | 703,582 | 703,582 |
Cooling Capacity(kW) | 2,474,499 | 2,474,499 |
Energy Consumption (kWh) | 16,519 | 824,833 |
Energy Cost (PHP) | 145,151 | 7,247,808 |
Annual electricity savings: 808,314kW/h
Annual savings in electricity costs: 7,102,657PHP /126,905USD
Payback Period: 10 months
Making the Best Product with Highest Standard, Yangzi Petrochemical, BASF
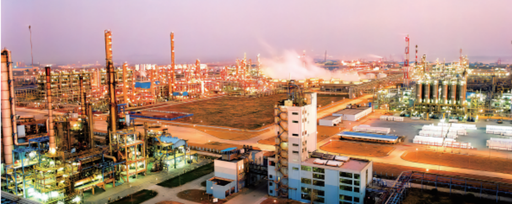
Yangzi Petrochemical-BASF Co. Ltd., a 50:50 Sino-German joint venture between Sinopec and BASF, is located in Nanjing and produces ethylene oxide and ethylene glycol, requiring stringent safety measures.
After a rigorous screening of refrigeration equipment suppliers, including six technical exchanges and site visits, BASF’s technical experts selected BROAD for its superior R&D and manufacturing capabilities. Consequently, Yangzi-BASF decided to use a BROAD single-stage hot water chiller for process cooling at their EOEG plant.
- Project Features
This project uses 98°C steam condensate generated during the production process to drive a hot water absorption chiller to produce 7MW of 16°C chilled water for process cooling of the EOEG unit. The chiller is installed in an explosion-proof area: ExdeibⅡBT4 and IP55 for electrical protection. Due to the importance of safety, there are high requirements for the chiller in all aspects.
2. High Relaibility
The chiller is used for process cooling, and the plant runs continuously 24/365, and can only be shut down during plantwide overhauls. The equipments on site are very compact and there is no dedicated room for the chiller, which can only be installed close to the production equipment. Due to the limited area of the site, only one chiller can be installed, which means that there is no possibility of a backup unit, and the only chiller must be guaranteed to run all year round. If the chiller failed and shut down the production process, the direct loss would exceed $1 million per day
3. High Stability
The chiller, placed outdoors with only a rain-proof shed, must operate stably in temperatures from -14°C to 43°C, with a heat source temperature of 98°C to 105°C and cooling water temperature of 26°C to 35°C. Despite significant temperature variations and poor-quality, corrosive cooling water from the plant’s system, the chiller must maintain a cooling capacity deviation within 4% and use anti-corrosion materials to ensure a design life of over 30 years.
Strict Manufacturing Standards
“Made in Germany” signifies the highest manufacturing standards, and to meet these, the chiller must adhere to BASF’s nearly 1,000-page specifications, far exceeding national standards. Fluor (China) reviews all process documentation, and Modi (Shanghai) Consulting Company conducts third-party inspections, ensuring rigorous quality control throughout manufacturing, including welding, material composition, non-destructive testing, and performance testing, with over a dozen BASF-YPC experts witnessing critical tests.
Complete after-sales service system
Another important reason for Yangzi-BASF to choose BROAD is its excellent after-sales service. In particular, the BROAD global monitoring system plays an important role in the stable operation of the project. This system monitors and analyzes the chiller 24/365, and automatically connects to the terminal when a fault symptom or failure occurs, notifying service engineers to come to the site to solve the problem in a timely manner.
Project Operation
The chiller, operational since 2011, has not experienced any downtime due to failure for over 10 years, needing vacuuming only once every 1.5 to 2 years, unlike others that require it every few days. This project not only saves the customer over $1.6 million in energy costs annually but also demonstrates BROAD’s exceptional manufacturing, process, and after-sales service levels, meeting the high standards of Yangzi-BASF and exceeding their expectations.
Hankook Tires Factory, Tennessee
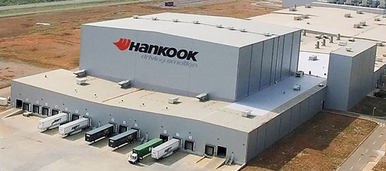
Founded in 1941, Hankook Tire has developed a global presence through continuous innovation and development over the past 80 years. In addition to its global headquarters in Korea, Hankook Tire has three regional headquarters (China, Europe and the USA) around the world. It invests 5% of its annual revenue in research and development and has established five R&D centres around the world to develop advanced technologies. This project is located in Tennessee, USA, and the client has planned to build the second phase of the plant.
Waste Hot Water Recovery Reference
Schematic System
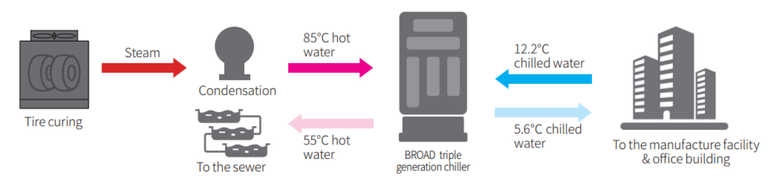
Waste Hot Water Recovery Reference
System Introduction
The plant utilizes waste steam from the tire curing process and a BROAD BDH250 Double Section chiller to recover 185°F (85°C) hot water for cooling the factory and offices, chilling water to 43°F (5.6°C) and reducing the heat source to 131°F (55°C), effectively using the waste heat.
Application Value
Recovered residual heat from steam condensate using BROAD Triple Generation chiller technology for process and office cooling, reducing power consumption and saving 1,060 tons of standard coal annually, which lowers carbon emissions by 2,642 tons—equivalent to planting 144,000 trees.
Food industry reference
The time of low-temperature heat sources
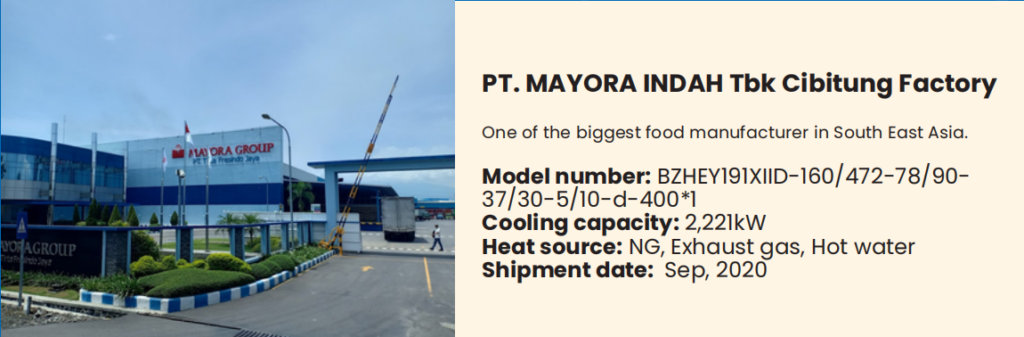
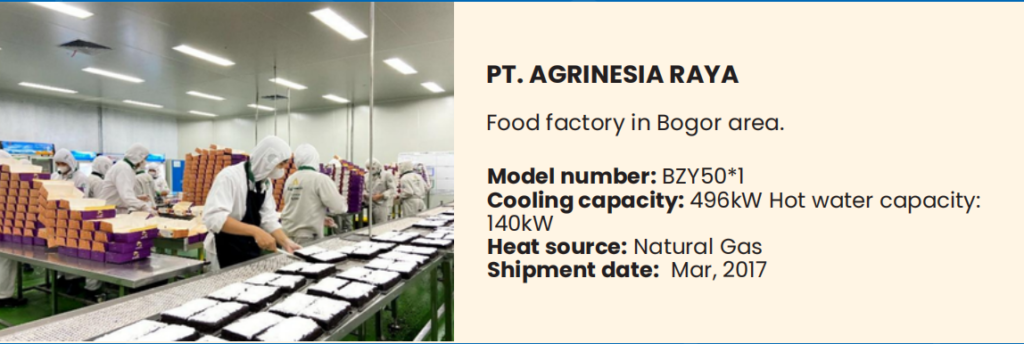
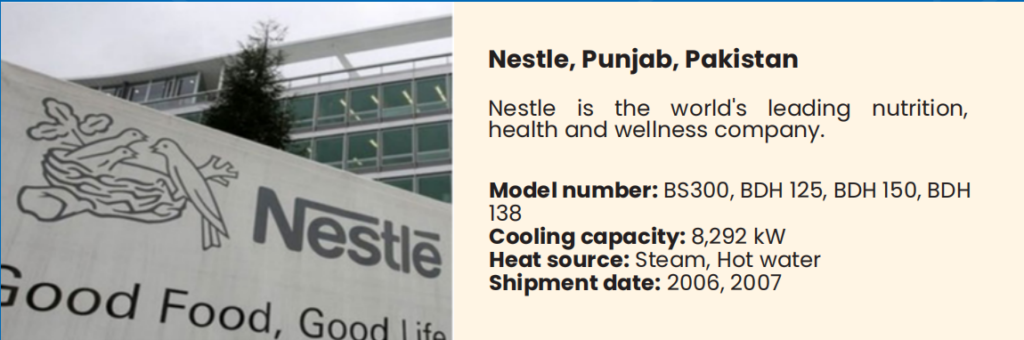
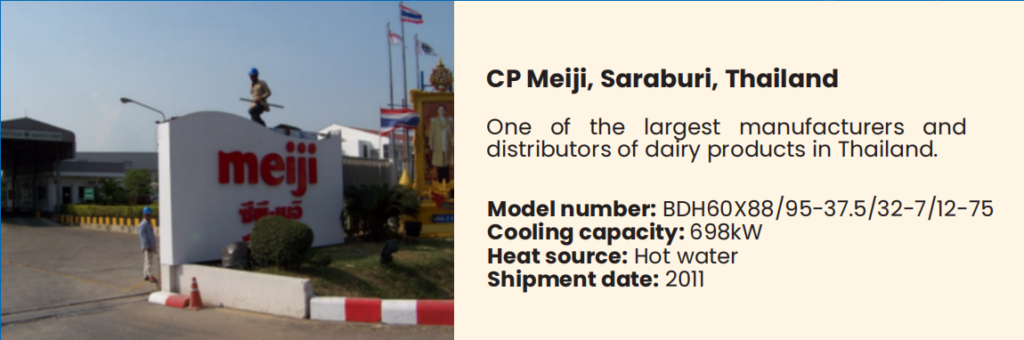
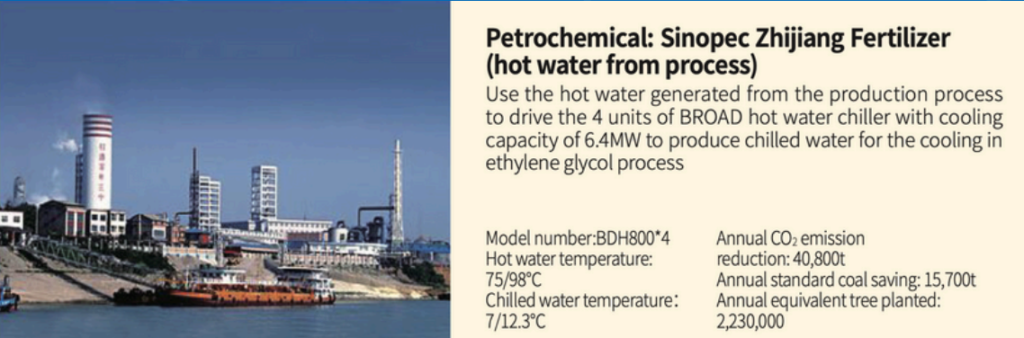
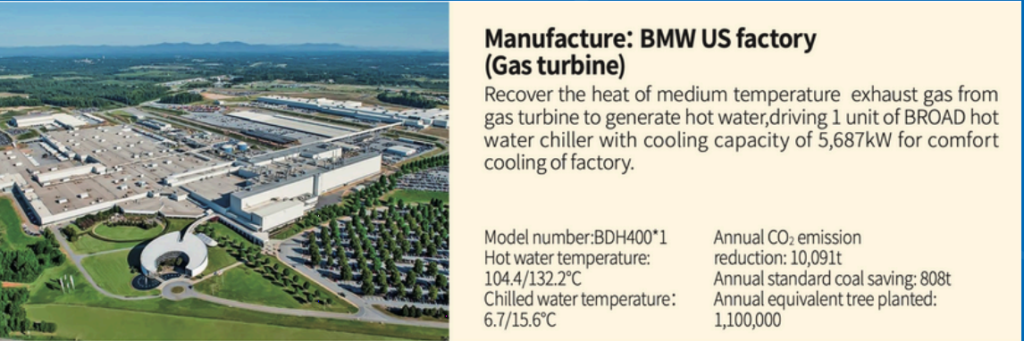
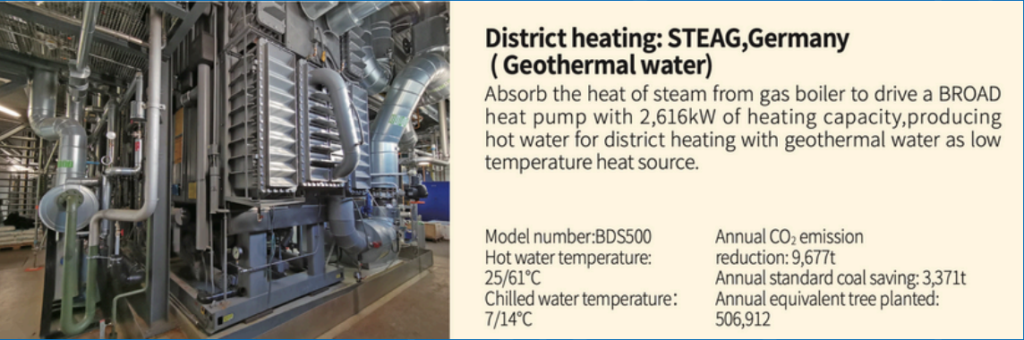
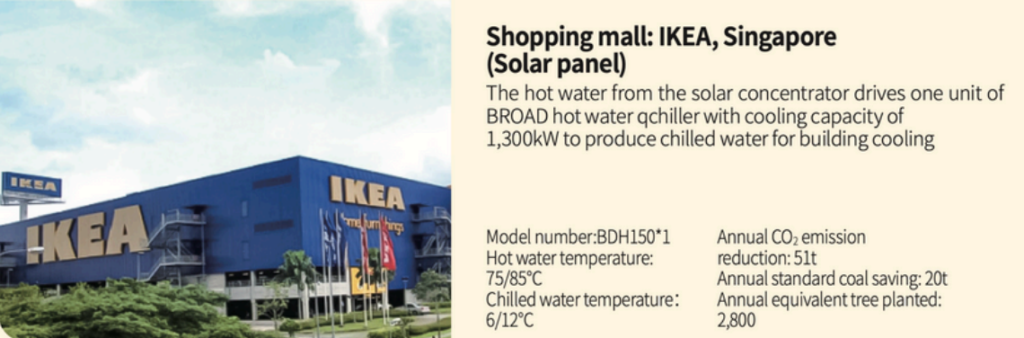